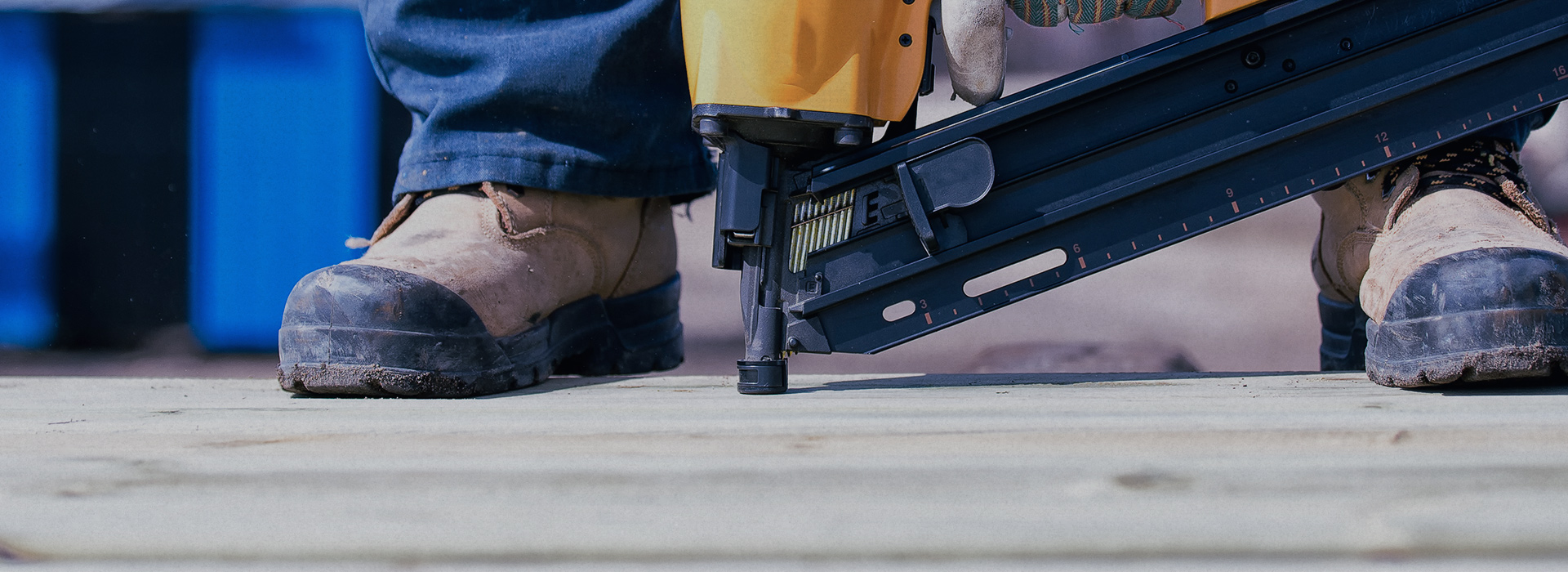
Our Commitment to Safety
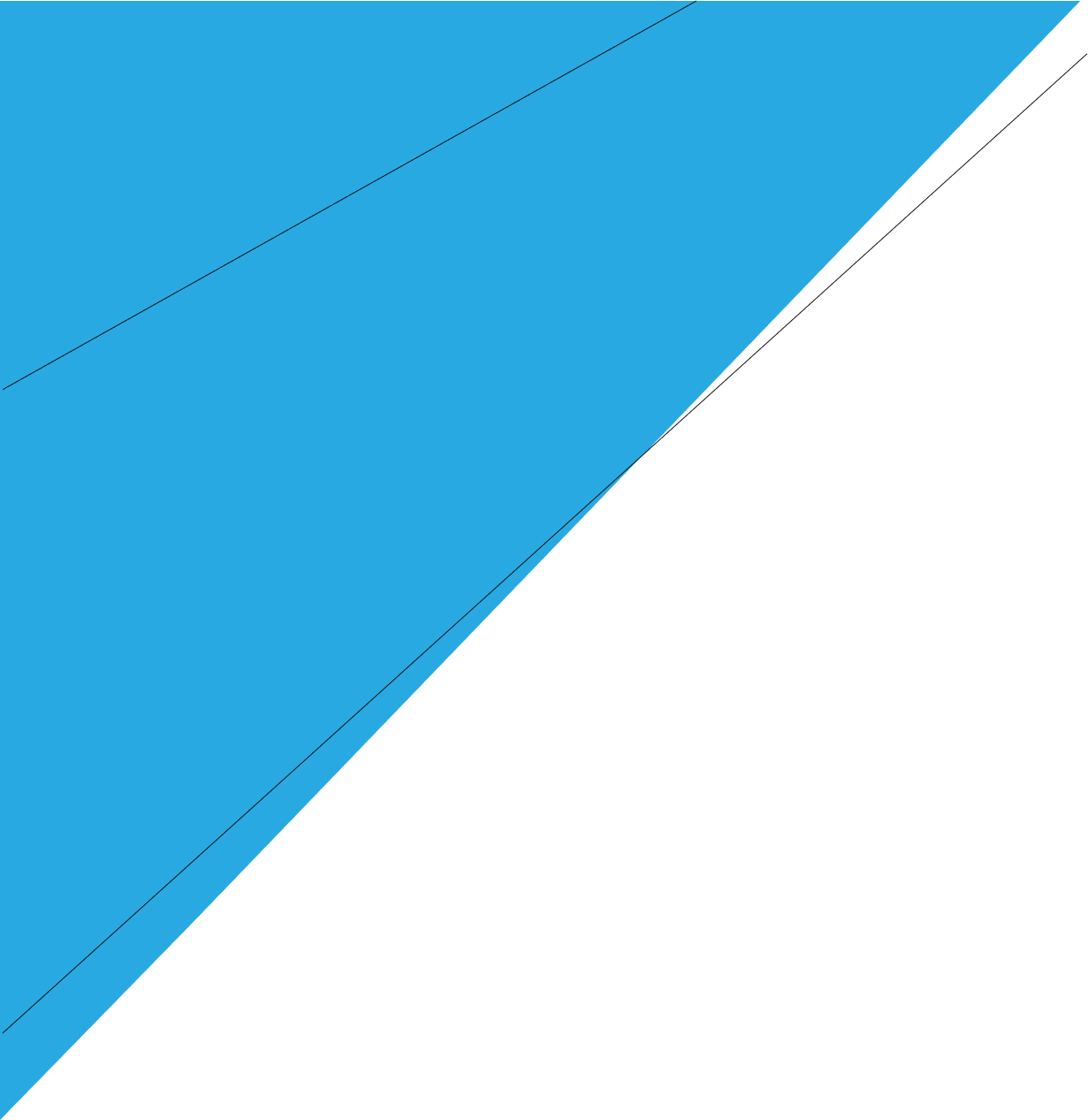
Everyone Goes Home Safe
State Group’s safety mantra, “Everyone Goes Home Safe”, promotes a work environment where everyone takes responsibility for their safety and that of others. Every project, every location, safety is our priority.We are very proud of our award-winning safety performance in both the United States and in Canada. We believe each customer and project is unique. We use our expertise to evaluate and mitigate risk factors to create safe work environments designed specifically for each project. We work with our customers to meet project timelines and budgets while keeping safety as a priority. We maintain our excellent safety record with the local labour and safety authorities. Our comprehensive safety management system is designed to ensure our workers adhere to the highest safety and quality standards.
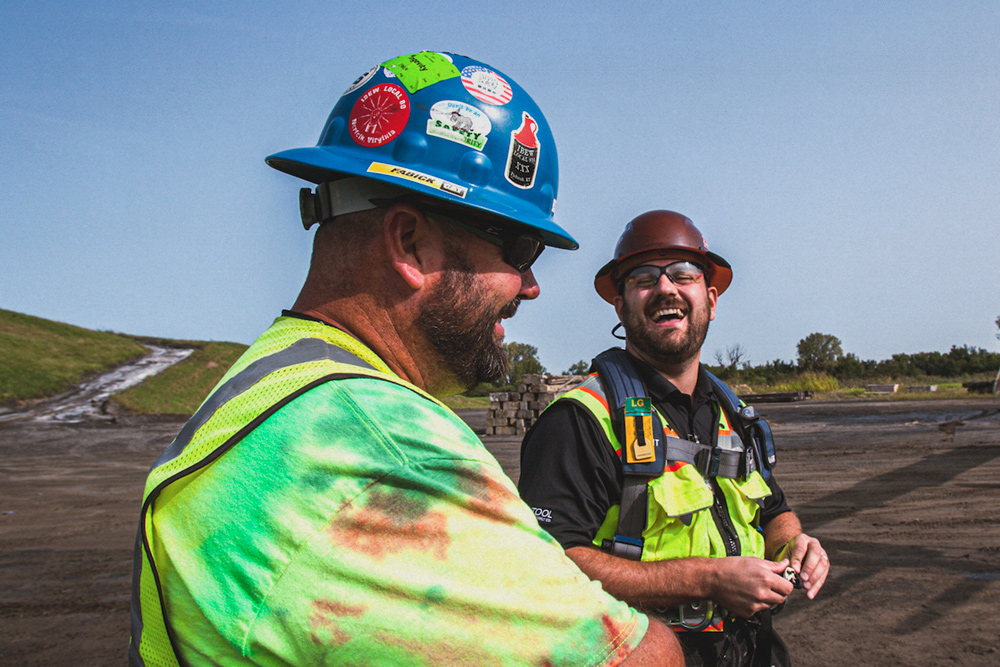
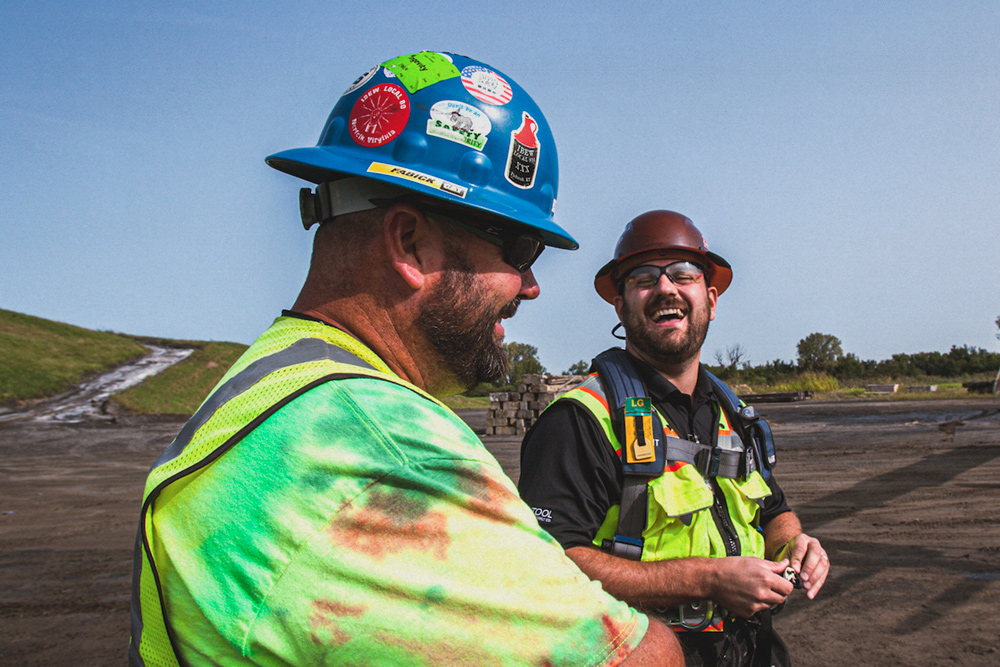
Our Cardinal Rules
To ensure ‘everybody goes home safe’, we’ve codified our commitment to on-the-job safety in ten simple rules.
Our Pillars of Safety
Planning
At the onset of a project, we perform project hazard assessments, identify risks and implement control measures. During the project, we perform daily job safety analyses that enable us to identify new hazards that may arise and control them to ensure that work is done safely.
Communication
Our communication system ensures timely, proficient, organized, and appropriate responses, easy dissemination of information, collaboration and participation between all stakeholders across our sites.
Continual Improvements
Our safety culture of continuous improvement allows us to incorporate industry best practices to ensure the safety of our employees and our clients. We also collect and analyze data from projects to improve our safety processes.
Training Management System
We have a unique and proprietary Training Management System called “Training Tracker” which administers online training (including test) and provides certification/confirmation of test completion stamped with the date. It also tracks all health and safety training completed by the worker. To complement the Training Tracker, we have a mobile app that is used for on-site management of all personnel on a specific project. The mobile app simplifies the process for safety log-in. It also provides on-site information for each worker on the training he/she has received.
Training & Development
We provide comprehensive training, including orientation, job-specific training, toolbox talks, first aid training, training on the use of PPE. Our trained coordinators and supervisors are equipped to empower the workers and provide relevant guidance and supervision. We provide our customers with highly trained safety personnel, trained through our internal apprenticeship program, to preserve our culture and commitment to safety.
Safety Audits and Monitoring
Our inspection, audit, and maintenance programs, aided by our comprehensive reporting and records-keeping, enable monthly analysis to identify trends and determine the need for potential revisions to our programs and/or policies. In addition to this, management conducts an annual review of the system, goals, and objectives, to ensure their relevance to evolving business needs and environments.
Safety Certifications and Awards
Awards
- 2023 ZISA Gold Star Award – The State Group Industrial (USA) Limited – Alcoa Corporation
- 2023 ZISA Bronze Star Award – The State Group Industrial (USA) Limited – General Motors Tonawanda Engine Plant
- 2023 ZISA Bronze Star Award – Beltline Electric Co., LLC – Honeywell
- 2023 ZISA Bronze Star Award – Beltline Electric Co., LLC – Ashland ISP
- 2023 NECA Safety Excellence Recognition of Achievement – Delta Services, LLC
- 2022 ZISA Gold Star Award – The State Group Industrial (USA) Limited – Alcoa Corporation
- 2022 ZISA Bronze Star Award – The State Group Industrial (USA) Limited – General Motors Company Tonawanda Plant
- 2022 ZISA Merit Award – The State Group Industrial (USA) Limited – General Motors Company Lockport GMCH
- 2021 TAUC Thomas J. Reynolds Safety Award – Beltline Electric Co., LLC
- 2021 ZISA Gold Star Award – The State Group Industrial (USA) Limited – Alcoa Corporation
- 2021 ZISA Bronze Star Award – The State Group Industrial (USA) Limited – General Motors Company Tonawanda Plant
- 2021 ZISA Merit Award – The State Group Industrial (USA) Limited – General Motors Company Lockport GMCH
- 2020 ZISA Gold Star Award – The State Group Industrial (USA) Limited – Alcoa Corporation
- 2020 ZISA Merit Award – The State Group Industrial (USA) Limited – Ford Motor Company
- 2020 ZISA Bronze Star Award – The State Group Industrial (USA) Limited – General Motors Company Tonawanda Plant
- 2020 ZISA Merit Award – The State Group Industrial (USA) Limited – General Motors Company Lockport GMCH
- 2019 ZISA Gold Star Award – The State Group Industrial (USA) Limited – Alcoa Corporation
- 2019 ZISA Merit Award – The State Group Industrial (USA) Limited – Ford Motor Company
- 2019 ZISA Merit Award – The State Group Industrial (USA) Limited – General Motors Company Lockport GMCH
- 2019 ZISA Merit Award – The State Group Industrial (USA) Limited – General Motors Company Tonawanda Plant
- 2018 ZISA Gold Star Award – The State Group Industrial (USA) Limited – Alcoa Corporation
- 2018 ZISA Merit Award – The State Group Industrial (USA) Limited – General Motors Company Lockport GMCH
- 2018 ZISA Merit Award – The State Group Industrial (USA) Limited – General Motors Company Tonawanda Plant
- HHCA 2018 – 2020 Health & Safety Achievement Award
- ECAO R.H. Carroll Safety Award 2023
- ECAO R.H. Carroll Safety Award 2017
- MCA Toronto – 2015 Award of Merit
- Indiana Construction Association Gold Summit Zero Injury Pinnacle for 2009 – 2012
- TransCanada Pipelines Contractor Safety Award of Excellence
- ArcelorMittal Dofasco Zero Frequency Lost Time Injury Award (100,000 hours)
Certifications
- COR™ Certified, IHSA
- CSS Safety Certified Contractor
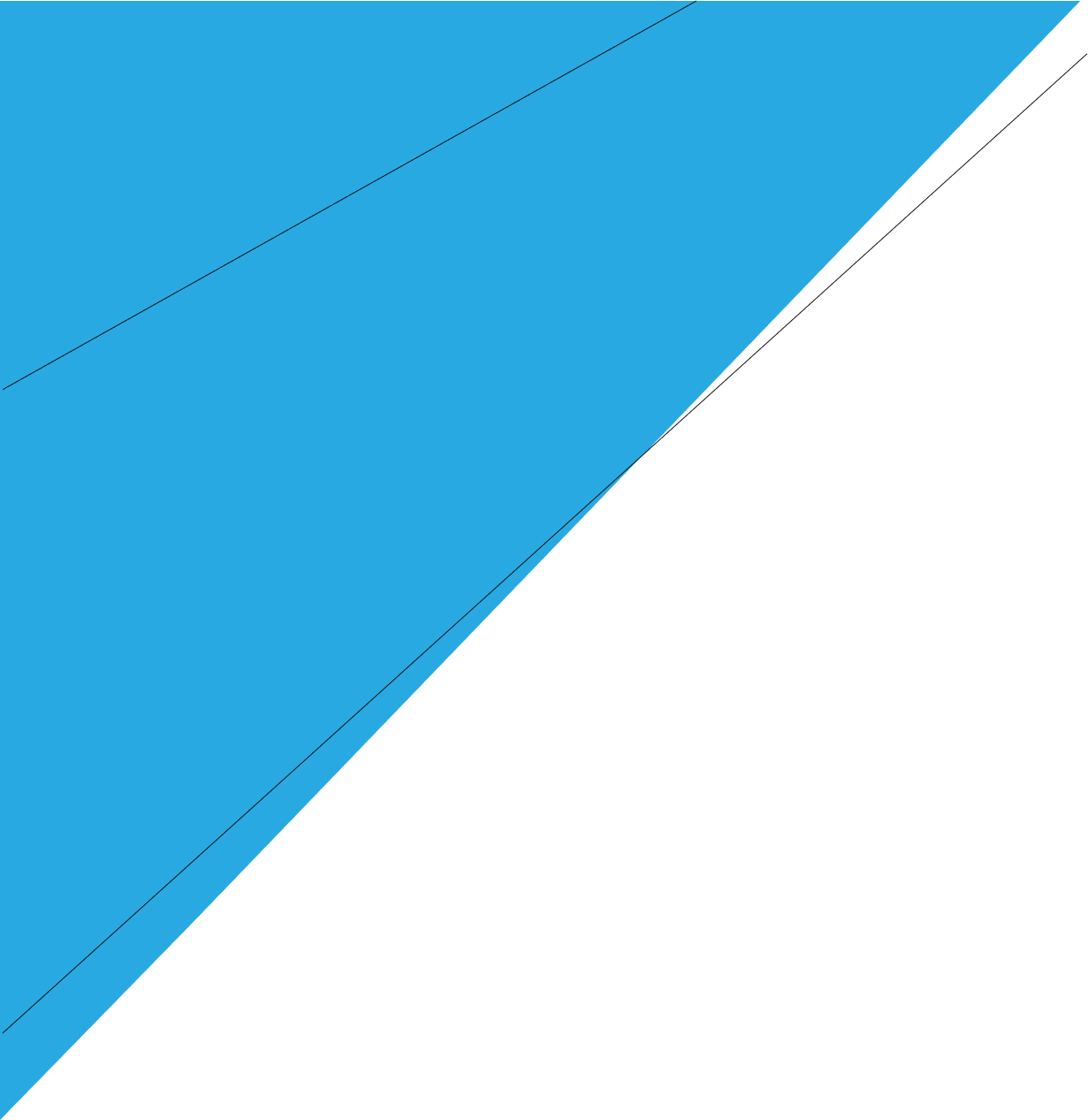
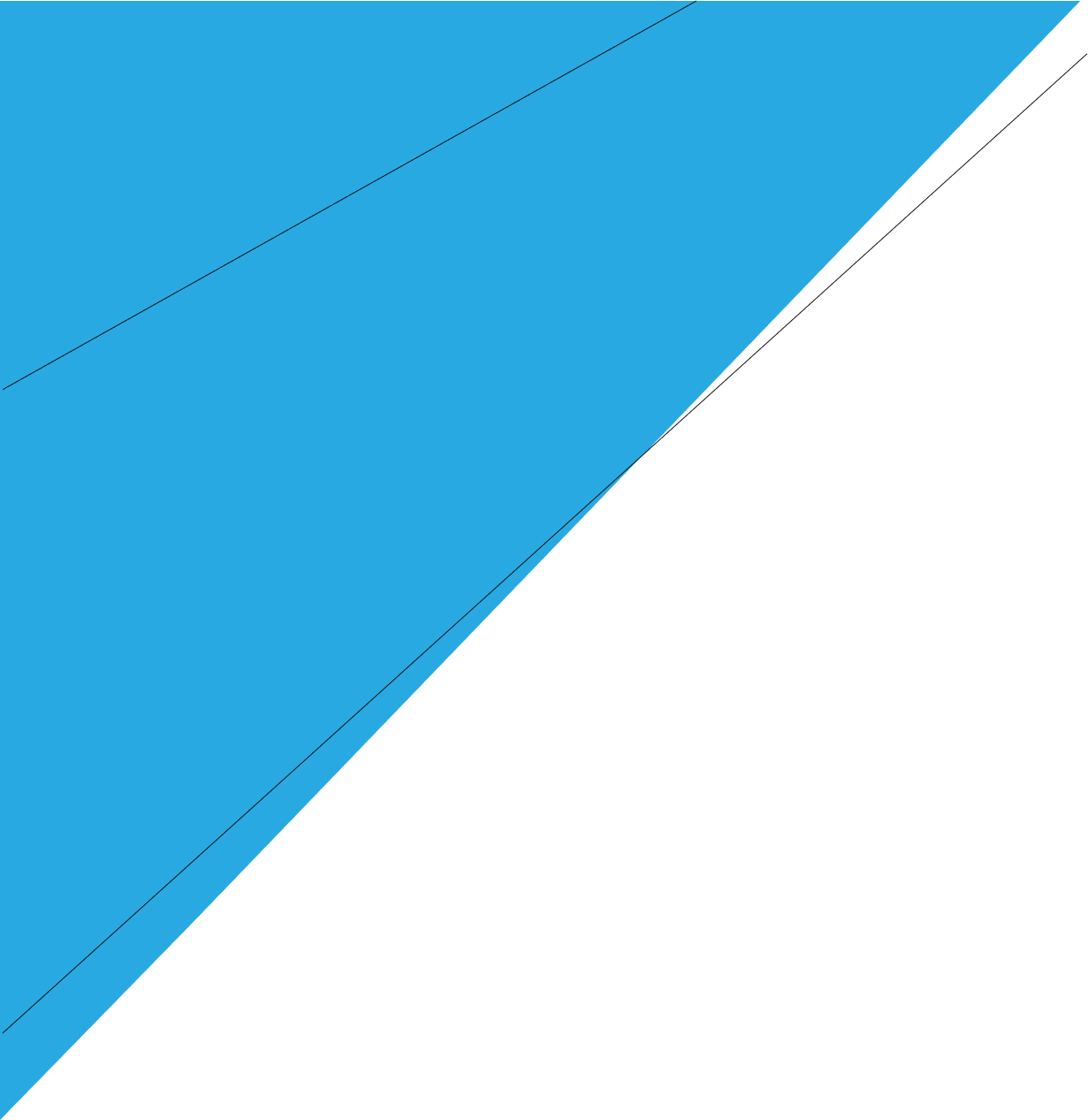
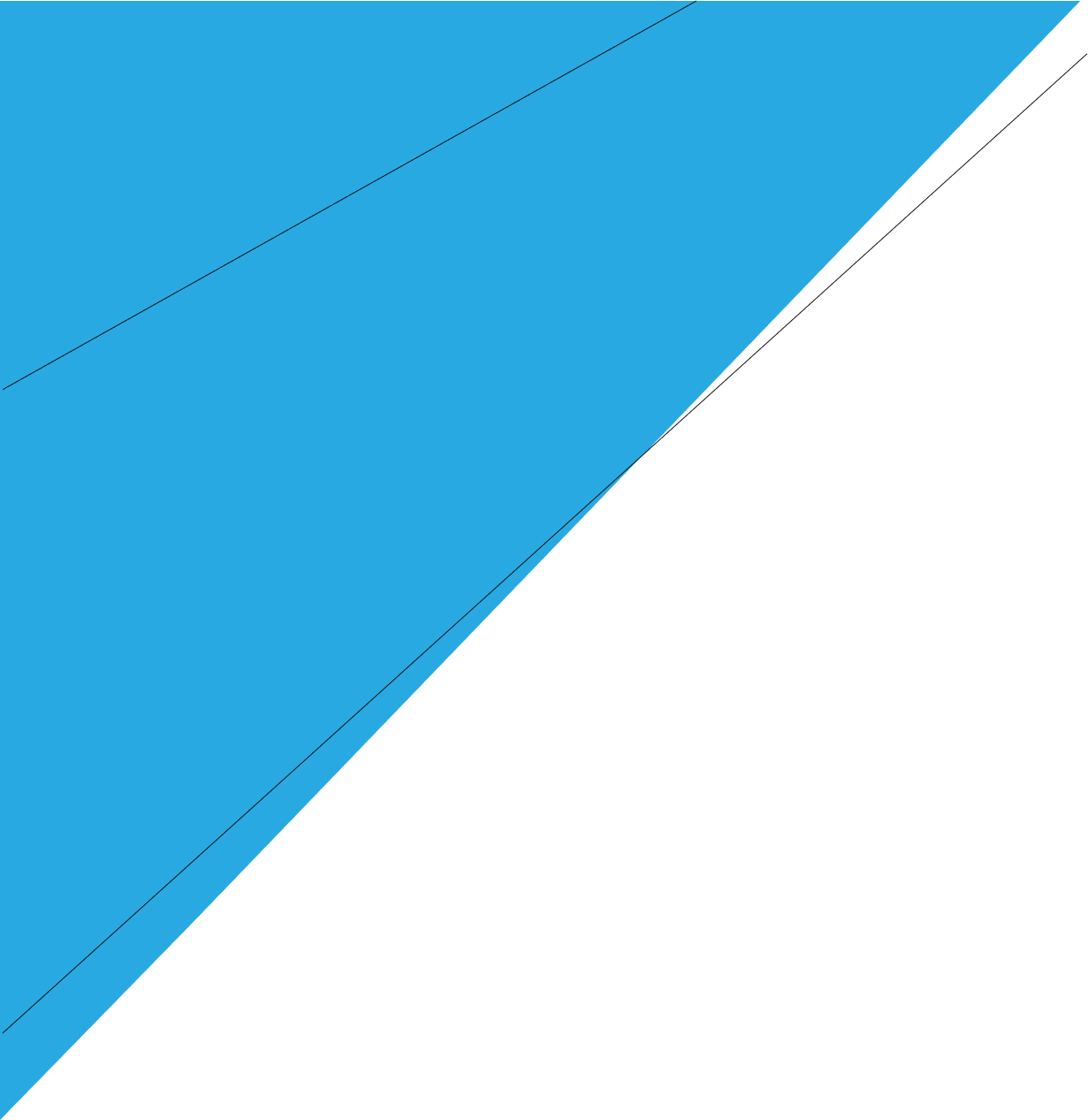
Safety & Emergency Training Services
To make workplace safety more approachable and accessible, The State Group offers comprehensive training modules in Safety and Emergency Rescue Services.
Safety Services
- NCCER Certified to provide Operator Qualification (OQ) training
- Fit testing (quantitative and qualitative)
- Elevated work platforms
- Forklift (construction)
- Working at Heights
- St. John Ambulance First Aid
Emergency Rescue Services
- Internal Confined Space Rescuers with equipment
- High-angle rescue
- Advance Medical First Responder
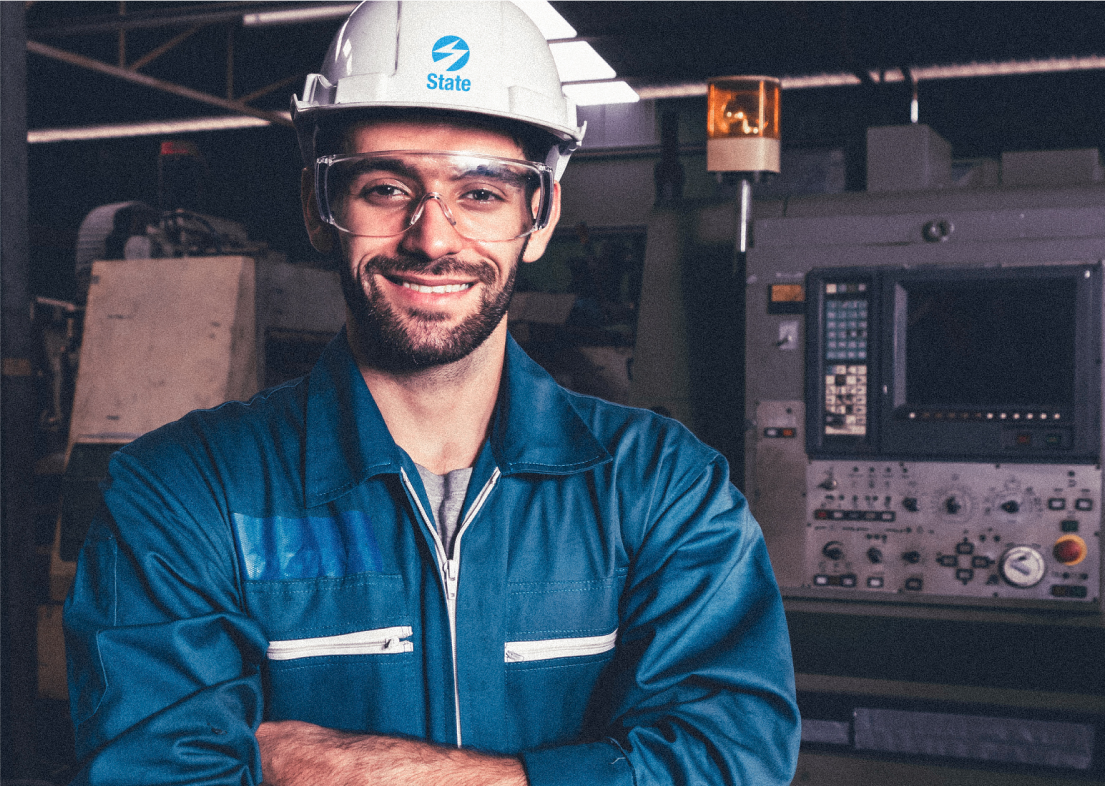